Defects can show up in casts for various reasons – some within and others outside your control. Knowing what to watch out for and which defects can be corrected will help ease the worries to some extent.
Defects are part and parcel of the casting game. Artists are aware that some defects are bound to appear in their casts for various reasons – some can be managed, some need to corrected while others can require making a new cast altogether. These defects can show up in all kinds of casts – be it made of plaster, sand, metal, polyurethane resin, latex rubber or even silicone rubbers.
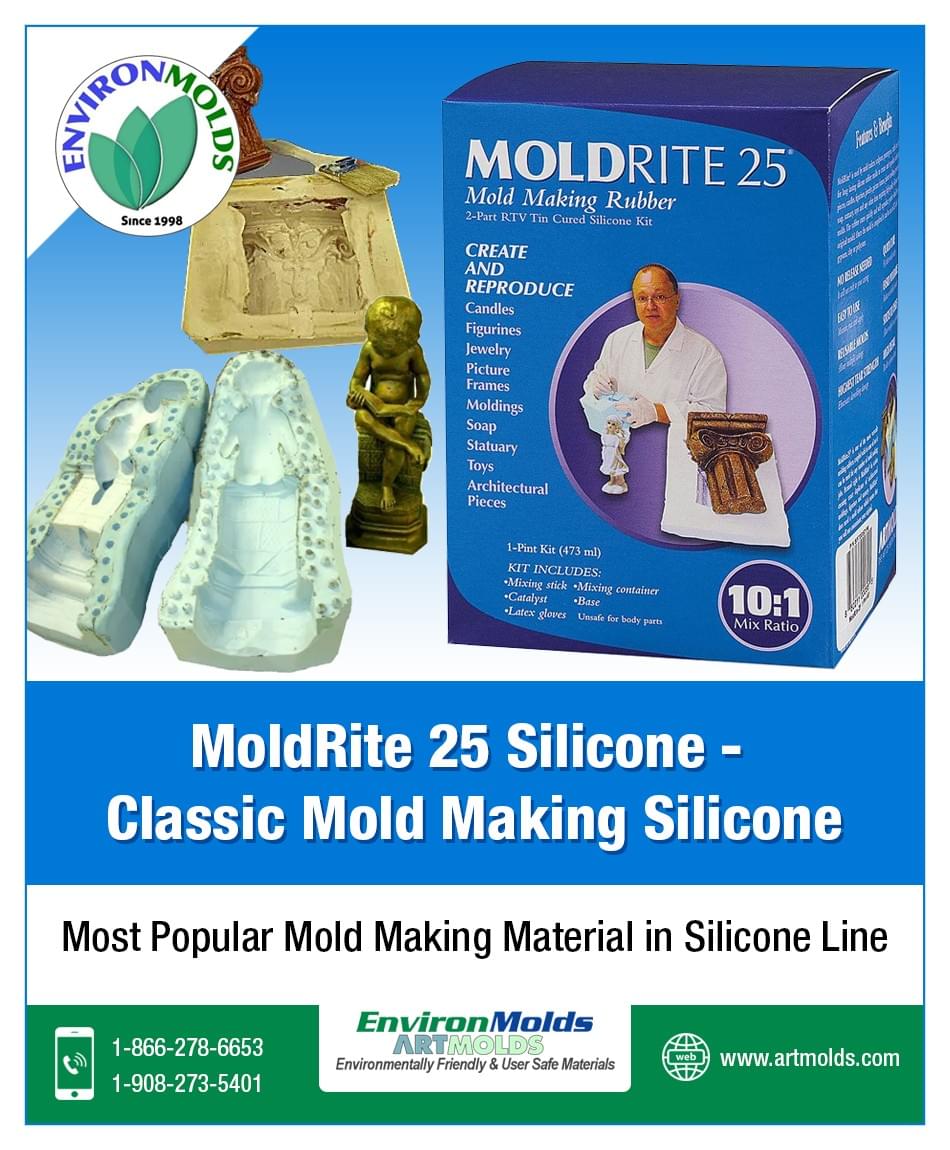
Let us take a look at the common types of blemishes that can mar a cast on occasion:
- Holes – These are tiny holes or indentations that appear on the surface of the cast or just below the surface at times. They are usually visible to the naked eye and are caused due to the presence of poorly vented pockets or even improper drying of the casting material. They can typically be corrected by scraping with sandpaper.
- Bubbles – Many casting materials tend to capture air that shows up as tiny bubbles on the surface of the cast. This is why artists usually deair the material or use other requisite precautions prior to casting. While minute bubbles are generally manageable with abrading, bigger ones will call for a repeat.
- Shrinkage – Some casting materials may pull back from the mold during the cure stage on account of their natural shrinkage properties. At times, the mold may absorb water from the casting material leading to shrinkage. Check if the shape remains the same and if the reduced dimensions are acceptable.
- Run out – The casting material may leak out of the mold leading to a faulty or incomplete casting. This can be due to faulty mold construction or even wear and tear from repeated use of the mold. It will generally require starting from scratch by making a new mold.
- Drops – These usually occur when dust, dirt or other debris happen to fall on the casting before it has cured. These will appear as irregularly shaped projections and can look unbecoming. It is better to keep the casting in a clean and safe place while it cures.
- Cracks – Tears and cracks are irregular crevices that can appear on the cast for various reasons ranging from improper mixing of the casting material to moving and shaking the cast before it has set. It can generally be covered with a thin coat of casting material.
- Mismatched cast – In case a two-part or multi-part is not aligned properly prior to the casting, the cast can turn out distorted or shifted. This cannot be corrected and will call for a redo while taking care to join the mold parts properly.
There are many more types of defects that can spoil a cast. It is advisable to use good quality mold making and casting materials – like MoldRite 25 Silicone and Pliatex Casting Rubber – and exercise caution at all times.