Making a two part mold may appear complicated for beginners, but casting in the same is truly a breeze for everyone! Just brief yourself over the simple steps and you will be ready to cast as you wish.
It is customary to make multi-part molds for casting complicated objects that do not have a flat base or feature too many undercuts. As the model cannot be glued down to a flat surface, the answer lies in making two part molds.
As the name goes, the mold cannot be made in one go. It is usually made in two or more parts which will later come together to form the full mold. The process involves embedding half of the model in clay and placing it in a mold box before pouring the mold making material over it to make half of the mold. The basic steps of cleaning, sealing and applying a release agent are mandatory here.
Once cured, the model is removed from the clay and turned around to make a mold of the other half. Before this, the mold maker will make keys in the first half and also embed a straw or other object to make a spue or spout.
The other part of the mold is also made in a similar manner. Once cured, the mold is carefully cut from the spue hole and down the middle till the model can be extracted from within. Alternatively, the first mold part can be separated earlier on.
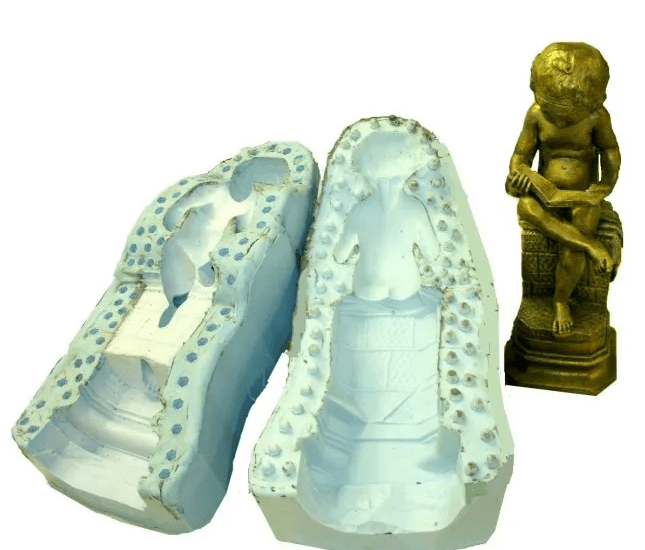
How to make the cast?
The two parts are joined along the keys and fastened with heavy duty bands to ensure that they stay together without any leakages. Now the mold is ready for casting. The casting material – be it plaster, wax, resin or rubber – can be poured from the spout till it fills the mold to the brim.
Allow it to cure properly before removing the bands and separating the mold parts. The replica cast is ready in its entirety. Any extra bits of casting material or lines on the cast can easily be buffed, scoured or cut from the cast. Finish it as desired and it will be ready for use/display.
Here, it is also possible to make faux replicas of the model in a variety of metals, stones, ceramic or even wood. A range of cold casting powders are available that can be mixed in the casting resin before pouring into the mold. For bigger pieces, it is more cost-effective to brush, slush, dust or spray the cold casting powder directly on to the cast to create a thin coating on the surface. This will replicate the original look so well that it will be nearly impossible to tell that it is a faux reproduction.
A renowned art supplier offers more detailed information along with step-by-step instructions on everything to do with how to make molds and casts. The tips for making complicated multi-part molds and especially life casts can prove to be very handy and useful.